Grinding & Sanding
Outstanding Surface Quality
Sanding and grinding are crucial processes in sheet metal fabrication. Learn about the benefits of sanding and grinding sheet metal, the different types of sanding and grinding techniques, and how to choose the right one for your project.
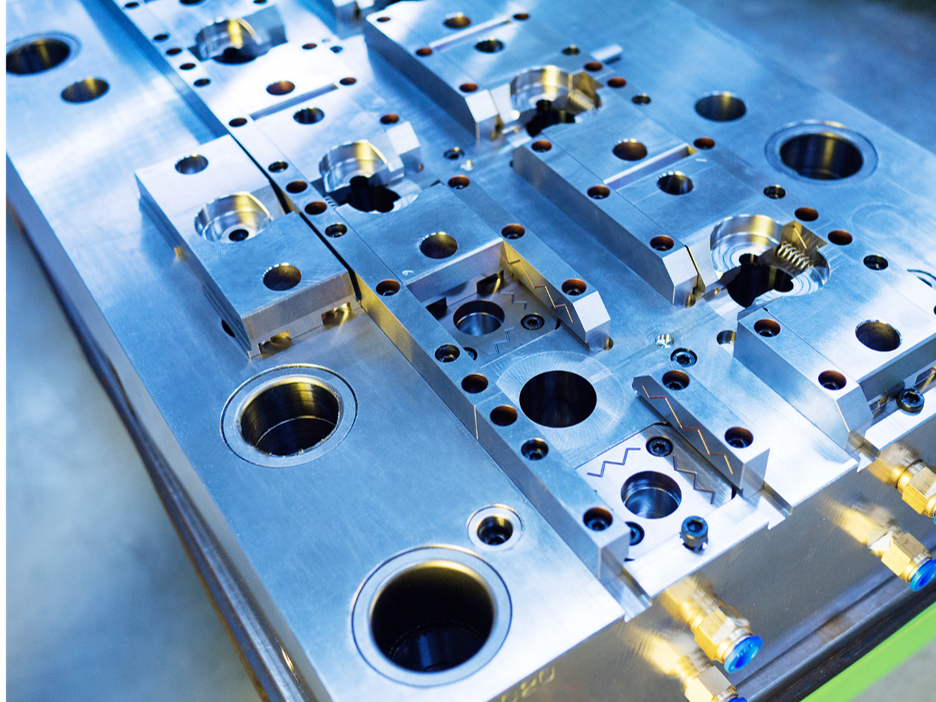
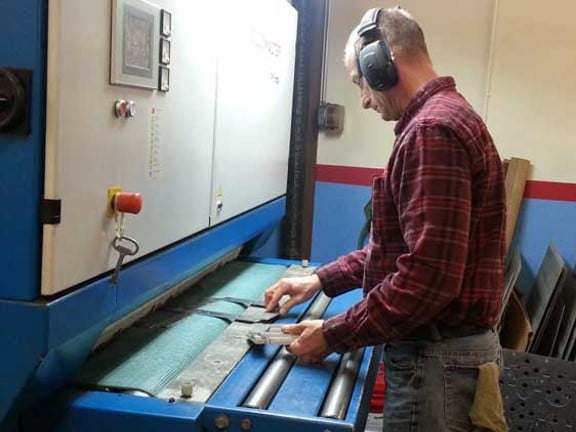
Sanding Sheet Metal: Benefits, Process, and Types
Sanding in sheet metal fabrication is a finishing process used to smooth out the surface of the metal, remove imperfections, and prepare it for finishing such as painting or coating. This process is crucial for improving the aesthetics of the metal, ensuring its functionality, and enhancing its durability.
Benefits of sanding sheet metal:
- Surface smoothing: Sanding helps to remove scratches, dents, and other surface imperfections from the sheet metal.
- Preparation for coatings: A smooth surface ensures better adhesion for paint, coatings, and other surface treatments.
- Burr removal: After sheet metal has been cut using processes like laser cutting or punching, it often has sharp edges and burrs. Sanding helps to remove these, making the metal safer to handle and more visually appealing.
- Grain modification: Sanding can change the grain of the metal, helping to prevent cracking during forming and bending processes.
- Aesthetic enhancement: Sanding can be used to achieve specific surface finishes that contribute to the visual appeal of the metal part.
- Improved adhesion: A sanded surface provides better adherence for paint, coatings, and other surface treatments, leading to longer-lasting and more durable finishes.
Types of sheet metal sanding:
- Wet sanding: Wet sanding uses a water-based lubricant to reduce friction and heat generation. This results in a finer finish and less material removal.
- Dry sanding: Dry sanding does not use a lubricant. This process is typically faster and removes more material, but it can also lead to a rougher finish.
Choosing the right sanding technique:
The best sanding technique for your project will depend on the type of metal, the desired finish, and the amount of material removal required. If you are unsure which technique to use, it is best to consult with a professional sheet metal fabricator. Give EMS Fabrication a call, we'll discuss your needs and recommend a solution.
Sheet Metal Grinding: Everything You Need to Know
Grinding is a crucial process in sheet metal fabrication, used to improve quality, appearance, and functionality. An abrasive wheel or belt is used to remove material from a metal workpiece, resulting in a smoother and more refined surface. The most common use cases are:
- Smoothing surfaces
- Removing weld beads
- Deburring edges
- Creating sharp edges
Types of sheet metal grinding:
- Handheld grinders: Portable tools that can be used for large or hard-to-reach parts.
- Machine grinders: Stationary grinders that offer precision and are suitable for mass production.
- Belt grinders: Use a belt coated with abrasive material to grind surfaces and finish parts.
- Surface grinders: Create a flat and smooth surface on the metal workpiece.
Benefits of sheet metal grinding:
- Quality enhancement: Grinding ensures that the metal parts meet the required standards of quality and finish, enhancing performance and longevity.
- Aesthetic improvement: A well-grounded piece has an improved appearance, which is crucial for parts that are visible in the final product.
- Preparation for further processing: Grinding prepares the metal surface for additional processes such as painting or coating, ensuring better adhesion and results.
Conclusion:
Grinding is a critical process in sheet metal fabrication, enhancing the quality, appearance, and functionality of metal parts. At EMS Fabrication, we leverage a variety of grinding techniques and equipment to ensure that each part meets our high standards and satisfies our clients' specifications.
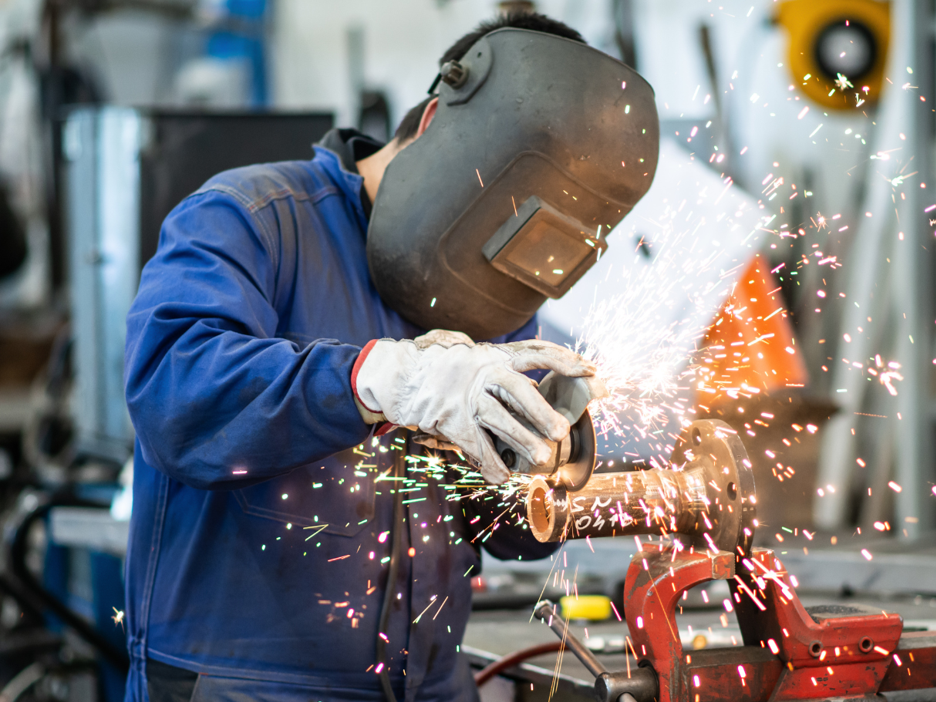
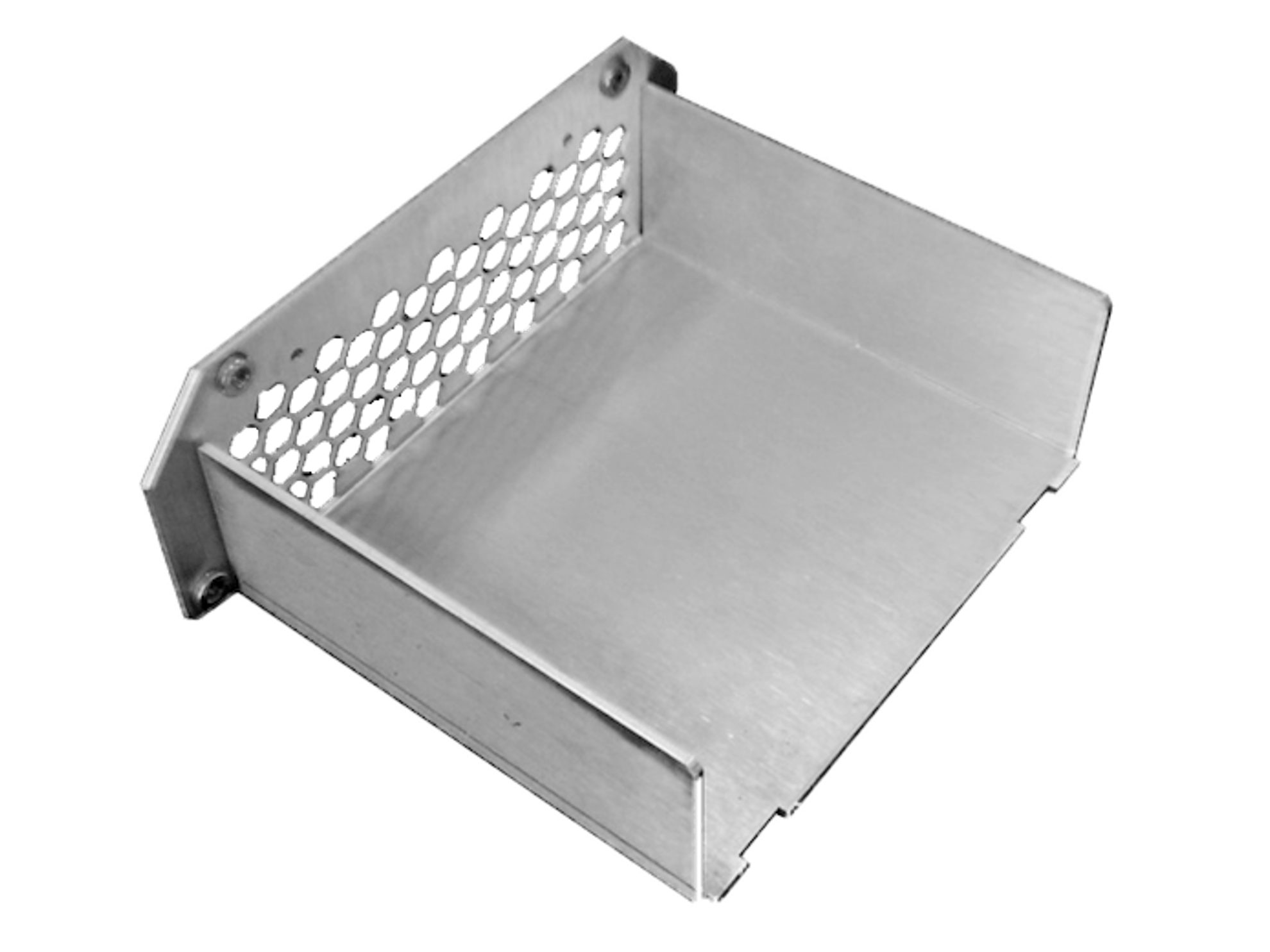