Welding
Welding Services at EMS: Quality Craftsmanship
EMS Fabrication offers comprehensive welding services, including TIG, MIG, and spot welding. Leveraging our team of highly skilled welders, we'll deliver exceptional results, meeting the specific needs of your project.
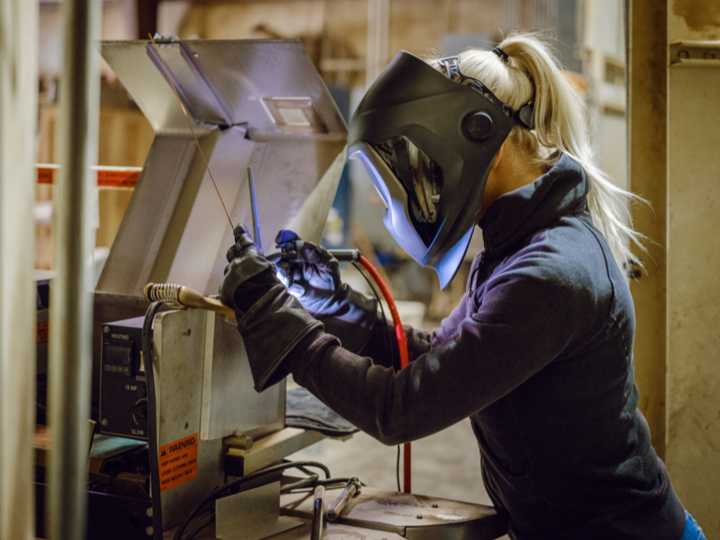
TIG Welding (Tungsten Inert Gas Welding)
TIG welding is a precision welding process that uses a non-consumable tungsten electrode and an inert gas shield to produce high-quality welds. It is ideal for a variety of materials, including stainless steel, super-stainless, hastelloy, aluminum, and other non-ferrous metals.
Key features:
- Precision: TIG welding offers unparalleled accuracy, making it ideal for intricate and complex welds.
- Versatility: TIG welding can be used to weld more metals than any other process, making it exceptionally versatile.
- Clean welds: TIG welding produces high purity welds, free from impurities and contaminants.
- Aesthetic quality: TIG welds have a smooth and clean bead appearance, often eliminating the need for post-weld finishing.
MIG Welding (Metal Inert Gas Welding)
MIG welding is a semi-automatic welding process that uses a continuously fed wire electrode and an inert gas shielding gas to produce high-quality welds. It is a popular choice for a variety of industrial applications, particularly with steel and aluminum.
Key features:
- Speed: MIG welding is faster than many other welding processes, providing high productivity.
- Ease of use: MIG welding is user-friendly, with a short learning curve, allowing for consistent, high-quality welds.
- Adaptability: MIG welding is suitable for a wide range of metal types and thicknesses.
- High efficiency: The continuous wire feed ensures a fast and uninterrupted welding process.
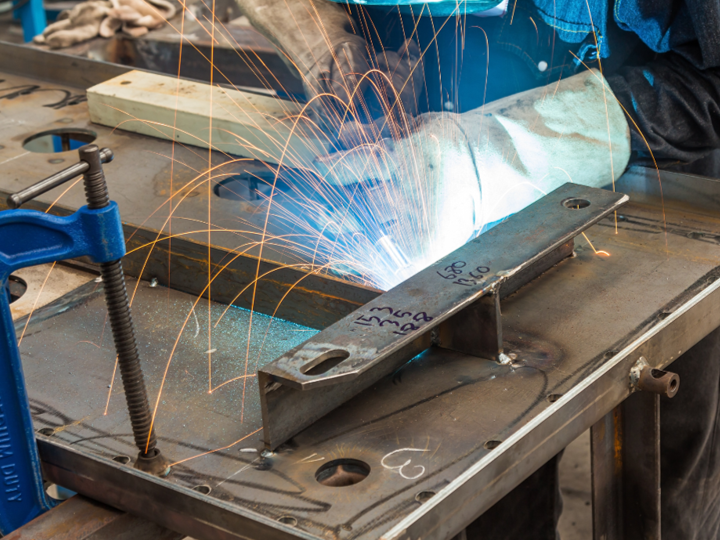
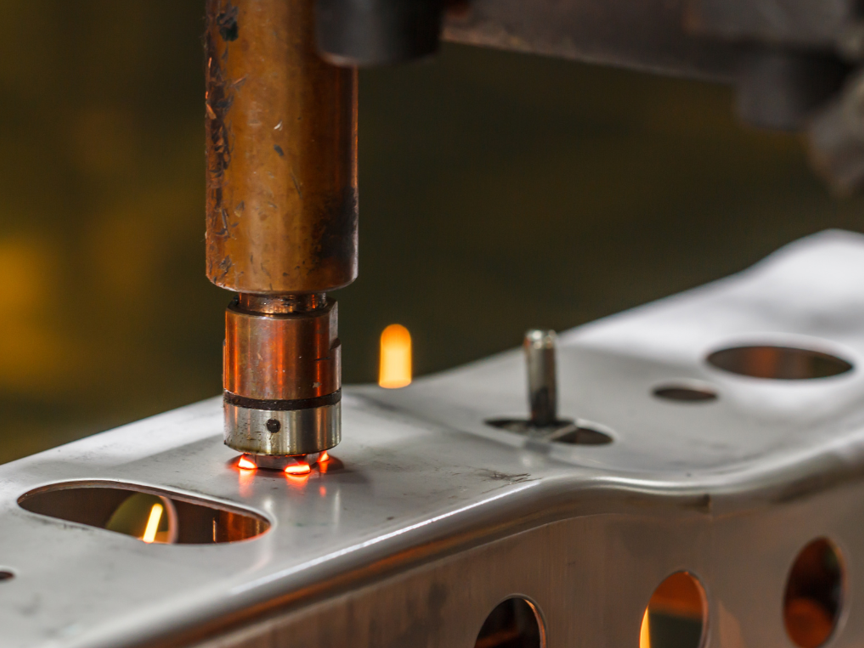
Spot Welding
Spot welding is a resistance welding process that uses two electrodes to apply pressure and current to localized areas of the workpieces, creating a strong bond.
Key features:
- Speed: The process is rapid, often taking only a fraction of a second to complete a weld. This speed translates to increased productivity.
- Strong & Durable Welds: The joints created by spot welding are typically robust and have high integrity, ensuring durability and long-term performance in finished products.
- Ideal for Welding Thin Metal Sheets: It's particularly effective for welding thin metal sheets, typically ranging from 0.5mm to 3mm in thickness. This makes it an ideal choice for automotive, electronics, and appliance manufacturing.
- Cost Effective: In addition to reduced labor cost due to the speed of the process, spot welding does not require filler material or inert gas.